Understanding the Importance of Durable Roofing for Industrial Buildings
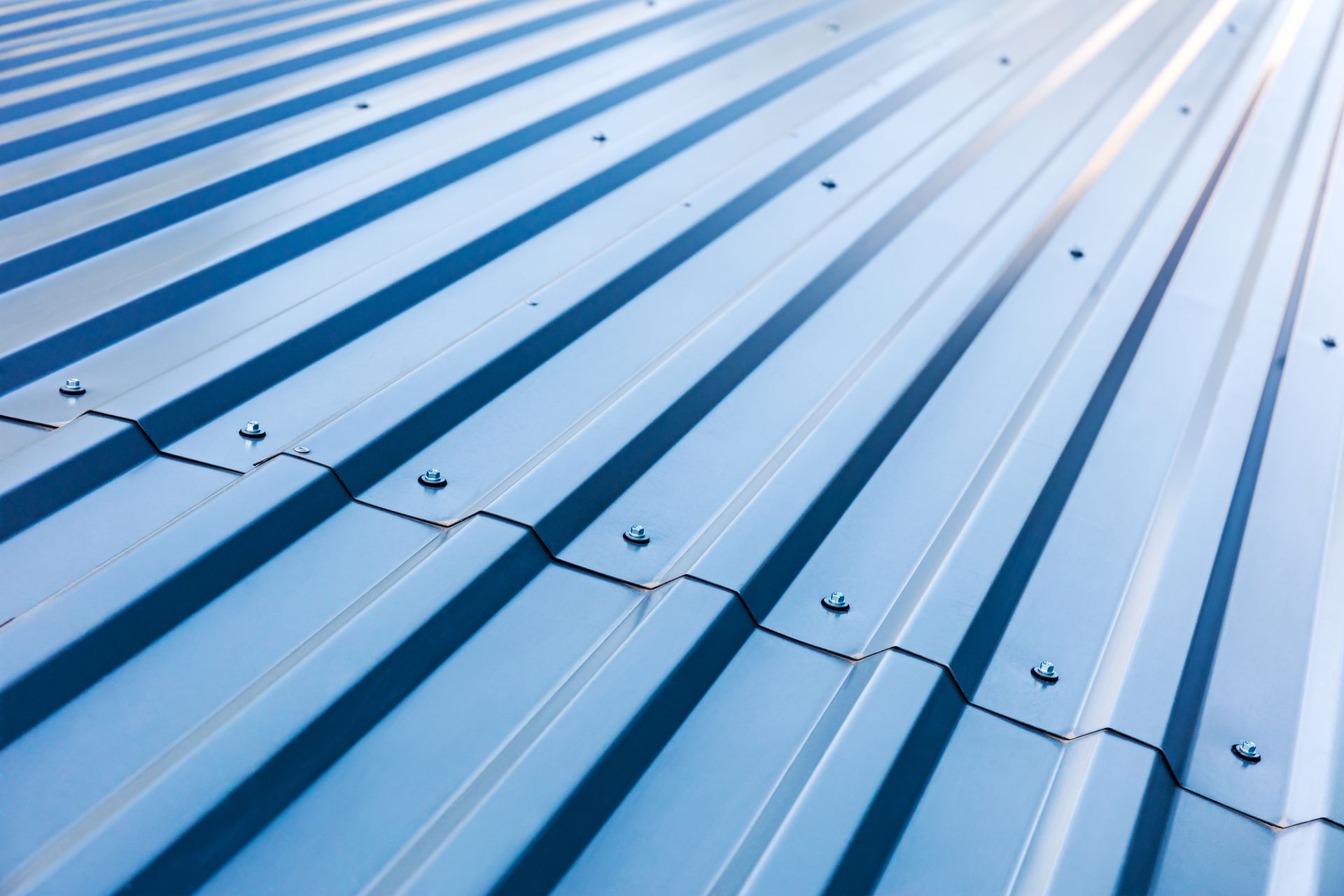
When the conversation steers toward the infrastructure of industrial buildings, the topic often centers around robust columns, spacious interiors, or cutting-edge engineering designs. Rarely does the spotlight turn to the unsung hero—the rooftop. Yet, in the hierarchy of industrial edifices, the durability and maintenance of the roof reign supreme, playing a direct role in facility management budgets, worker safety, and operational continuity.
Durability in your roofing ensures that the building's structural integrity and overall performance remain consistent, even in extreme weather conditions. The roof acts as a shield, protecting the interior from natural elements such as rain, snow, hail, wind, and sunlight. Without a strong and reliable roofing system in place, industrial buildings are vulnerable to costly damage and operational disruptions.
This expansive guide is crafted to educate industrial property owners and facility managers on the intrinsic value of employing durable roofing solutions. From weathering extreme environmental conditions to safeguarding against mechanical wear, we're unraveling the layers of industrial roofing—because what's above your head is as vital as what's under your feet.
Why Durability Matters in Industrial Roofing
Harsh Environment Conditions
Industrial environments are no strangers to the relentless forces of nature. Heavy industrial emissions laden with pollutants, exacerbated by high temps and chimneys releasing corrosive byproducts, create a perfect storm that standard roofing may not withstand. Durable roofing means standing tall against these elements, which can compromise safety and structural integrity over time.
Protection Against Mechanical Wear
Industrial rooftops are bustling workspaces, not just barren stretches of ceiling. Regular maintenance, service activities, and the equipment that dwells on top can lead to punctures, abrasions, and a host of mechanical stresses. This damage can lead to leaks, safety hazards, and even structural failure. A durable roofing solution provides a strong defense against these potential threats.
A sturdy, hardy roof is the difference between a minor inconvenience and a potential hazard.
Key Considerations When Choosing Industrial Roofing Materials
Lifespan and Long-term Costs
The decision to invest in a roofing system should always look beyond the upfront cost and consider the total lifecycle. Durable materials often demand a higher initial investment but frequently yield substantial savings over time due to longer replacement cycles and lower maintenance requirements.
When assessing the financial implications of different roofing materials, two primary factors are their expected lifespans and the total lifecycle costs. These aspects greatly influence the long-term financial outlook for businesses investing in industrial roofing solutions.
Metal Roofing
Metal roofs, made from materials like aluminum, steel, copper, or zinc, are renowned for their durability and longevity. They can last anywhere from 40 to 70 years with proper maintenance. Despite their higher initial cost, metal roofs offer lower lifecycle costs due to minimal maintenance needs and energy efficiency benefits. Their ability to reflect solar radiant heat can significantly reduce cooling costs.
Asphalt Shingles
Asphalt shingles are a common choice for less harsh environments and have an expected lifespan of 15 to 30 years. While the initial investment is comparatively low, the total lifecycle cost can be higher due to more frequent replacement needs and maintenance expenses. Asphalt shingles are less resistant to extreme weather conditions, which can lead to increased wear and tear.
Single-Ply Membranes
Single-ply roofing membranes, such as TPO, PVC, and EPDM, are tailored for flat or low-slope industrial roofs. These materials offer lifespans ranging from 20 to 30 years. The initial installation cost is moderate, but they provide value in terms of energy efficiency, especially with white or light-colored membranes that reflect sunlight. Maintenance and repair costs are generally low, contributing to a competitive lifecycle cost.
Monolithic Roofing
Monolithic roofing systems, such as spray foam and silicone coatings, offer a seamless and durable solution for industrial roofs. They have an expected lifespan of 20 to 50 years and provide excellent resistance against weathering, mechanical wear, and chemical exposure. With no seams or joints that can weaken over time, these systems require little maintenance and offer energy efficiency benefits.
Installation and Maintenance Requirements
Your choice of roofing materials dictates the installation complexity and, in turn, future maintenance. When it comes to industrial roofing installation, you can expect the process to be more labor-intensive and time-consuming compared to residential roofing.
Installation Complexity and Maintenance Commitments by Roofing Material Type
Metal Roofing
Installation Complexity: High. Metal roofing installation requires skilled tradespeople with specific expertise in handling and assembling metal panels or shingles. The precision in installation is crucial to ensure water tightness and durability. It involves intricate detailing around edges, penetrations, and terminations.
Maintenance Commitments: Low to moderate. While metal roofs are known for durability and longevity, they require periodic inspections to ensure fasteners and seams are intact, especially after extreme weather events. Recoating and repainting might be necessary to prevent corrosion and maintain aesthetics.
Asphalt Shingles
Installation Complexity: Moderate. Asphalt shingles are easier to install compared to metal roofing, making them a more common choice for less complex roof designs. However, proper installation is essential to avoid issues with moisture and to extend the lifespan of the roofing system.
Maintenance Commitments: Moderate to high. Regular maintenance checks are necessary to replace damaged or lost shingles and to address any issues with water penetration. Asphalt shingles may require more frequent roof inspections and maintenance due to their susceptibility to weathering and the potential for algae or moss growth.
Single-Ply Membranes.
Installation Complexity: Moderate. The installation of single-ply membranes is relatively straightforward, especially for large, flat, or low-slope surfaces where fewer penetrations and complex details are involved. It requires experienced roofing contractors familiar with the specific material, whether it's TPO, PVC, or EPDM.
Maintenance Commitments: Low. These materials generally demand minimal maintenance, primarily involving regular checks and cleaning to avoid debris accumulation and ensure drainage systems function properly. Any punctures or tears must be repaired promptly to maintain the integrity of the waterproof barrier.
Monolithic Roofing Systems
Installation Complexity: High. The application of monolithic systems such as spray foam and silicone coatings is a specialized process that requires professional application to achieve a seamless finish. It necessitates precise preparation and climate conditions to ensure proper adhesion and curing.
Maintenance Commitments: Low. Given their seamless nature, monolithic roofing systems typically require less maintenance. Regular inspections are recommended to check for any cuts or gouges that may need repairs. These systems also offer the advantage of being able to recoat them to extend the roof’s lifespan further.
For industrial business owners, understanding the balance between installation complexity and the long-term maintenance commitments of each roofing material is crucial. The right choice will depend on a variety of factors, including the building's design, the local climate, and the owner's budget and long-term facility management strategy.
Types of Durable Roofing Materials Suitable for Industrial Use
At ACR1 Commercial Roofing, we highly recommend a monolithic roofing system for your industrial building. This solution provides the perfect balance of durability, longevity, and low maintenance for industrial roofing needs.
Monolithic Roofing Systems
Monolithic roofing systems, renowned for their seamless and waterproof characteristics, are among the champions of resilience. They can withstand harsh conditions due to their exceptional strength, elasticity, and chemical resistance. Our monolithic roofing system is 3-4 times thicker than competitor materials, offering protection against items falling onto or thrown onto the roof and maintenance damage that screws or casings can cause.
Additionally, our Advantage Systems Roofing system is flexible, allowing it to flex with the movement of the structure and preventing damage. This flexibility is made possible due to the roof's self-flashing feature that allows it to form around 90-degree angles and circular items. This feature also prevents cutting and gluing, which helps prevent leaks and seam failure.
Strategies for Maximizing Roof Longevity
Regular Inspections and Maintenance
Routine inspections can catch small issues such as punctures, tears, or leaks before they become significant problems. These inspections should be conducted at least twice a year and after any extreme weather events.
Without regular inspections and maintenance, you risk extensive damage and costly repairs or even premature roof replacement.
Upgrades and Improvements
Age is not just a number when it comes to roofs—upgrades can be the lifeblood of longevity. Amplifying your roof's fortitude with technological advancements, such as protective coatings and enhanced structural supports, is a proactive step toward a more robust building envelope. At ACR1 Commerical Roofing, we offer a range of highly-reflective maintenance coatings, including:
- Flexbond White Elastomeric
- Flexbond Chips
- Flexbond Aluminum Coating
The Integral Role of Durable Roofing in Industrial Operations
Durable roofing isn't just a layer of protection; it’s a system that keeps the wheels of industry turning, regardless of the storm. Operational disruption from roof failure can lead to severe financial repercussions and, in critical sectors, implications for public safety and health.
Both on a micro and macro level, the decision to opt for a durable roof is a strategic one. It meets the basic requirement of shelter, yet beyond that, it’s an investment in the wellbeing of the business and its stakeholders.
The Financial Impact of Durable Roofing on Industrial Buildings
When we break down the numbers, the financial impetus for durable industrial roofing becomes crystal clear. The costs to repair or replace roofs in industrial settings are significantly higher than those in commercial or residential spaces, primarily due to their size and complexity. Warehouses, power plants, and factories can't typically afford to handle recurring or unanticipated roof expenses.
Choosing the right system doesn’t just save in replacement and repair costs. Energy-efficient roofs can reduce utility bills, and those savings can be substantial, given the sheer scale of industrial properties. An efficient maintenance strategy and a long-lasting roofing material guarantee the best return on the roofing investment.
Sourcing the Ideal Roofing Solutions
Selecting the ideal industrial roofing solution is not a one-size-fits-all endeavor. Each facility’s requirements are unique, and every solution must be tailored to this specificity. Consulting with seasoned professionals is paramount in navigating this critical decision-making process.
ARCI Commercial Roofing offers tailored consultations and premium solutions designed explicitly for industrial contexts. Our expertise, guided by a commitment to excellence, ensures a tailored approach to industrial roofing, from comprehensive assessments to the final sealing touch.
The Imperative of Durable Roofing in the Industrial Landscape
The roof over an industrial building reflects its core values—protection, continuity, and longevity. Durable roofing is not just a matter of construction; it’s a considerate investment in the narrative of your building’s legacy and functionality.
We implore every industrial property owner and facility manager who has embarked upon this educational journey to take the next step toward securing a durable roofing solution. Reach out to the experts at ACR1 Commercial Roofing today to get started!
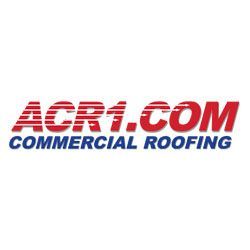
Author:
Floyd Mason
Born and raised in farming in Iowa
Worked in and around construction since 1977
BS in Corporate Finance and Financial & Estate Planning from Brigham Young University. Involved in Boy Scouts of America for more than 35 years, Scoutmaster 15 years Estimator, Project Manager, Sales Representative, Crew Leader, Laborer, Territory Manager, District Manager, Regional Manager, National Sales Manager,
ACR1.COM Sales & Marketing Manager since 2013.
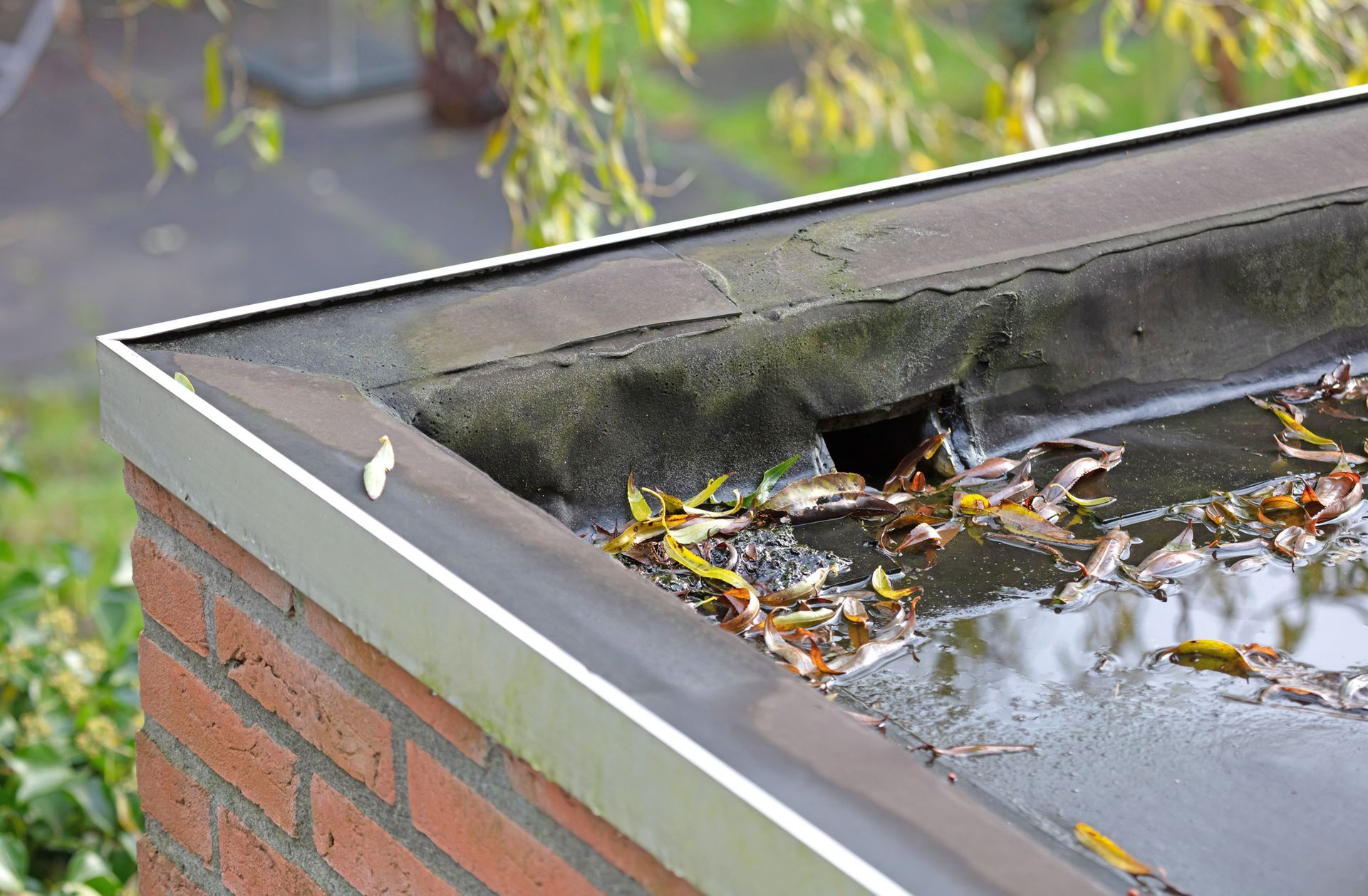